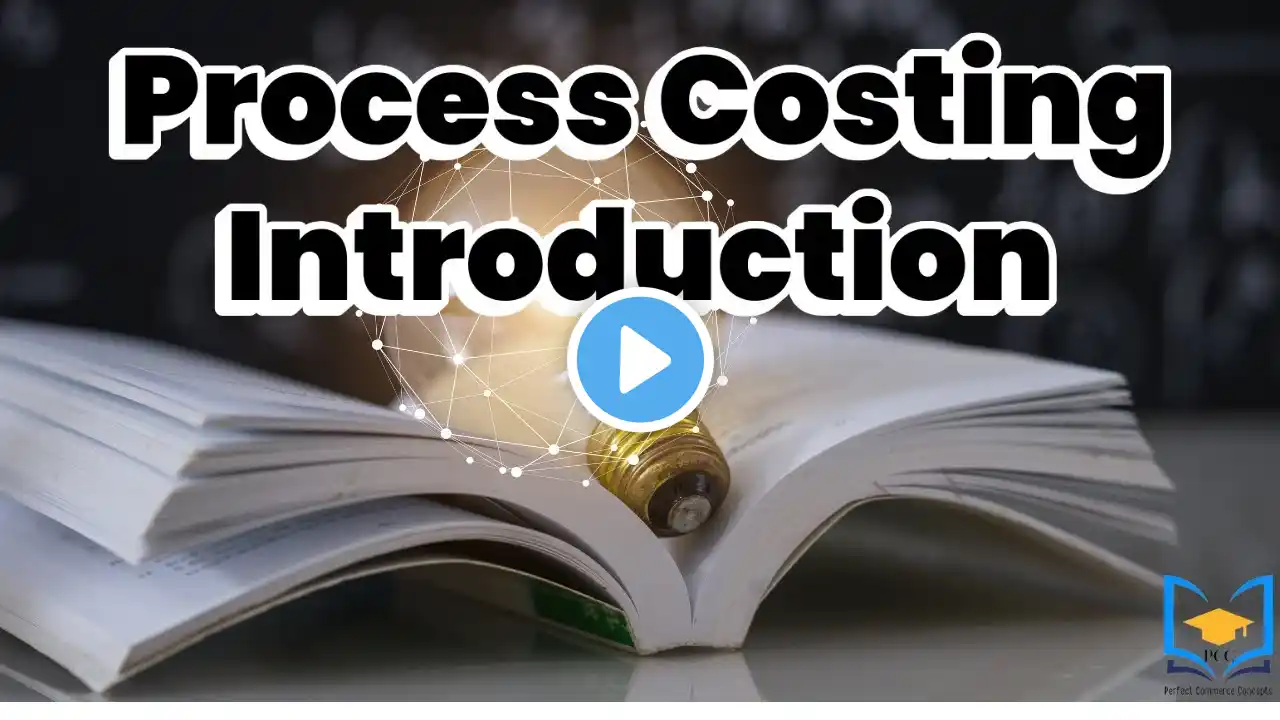
Process Costing Introduction | Cost Accounting | Costing |
Understanding Process Costing β Simplified for You! π Looking to learn about process costing in accounting? This video breaks it down step by step, making it super easy to understand! π‘ Whether you're a student, professional, or someone curious about cost accounting, this is the perfect guide to help you grasp: π What is Process Costing? π Key Features & Steps π Industries Using Process Costing π Practical Examples & Calculations Get ready to boost your accounting knowledge and ace your concepts! π π Don't forget to like, share, and subscribe for more educational content! #ProcessCosting #CostAccounting #AccountingBasics #CommerceStudents #FinancialManagement #LearnAccounting #ProcessCostingExplained #AccountingConceptsProcess Costing A Simple Explanation Process costing is a method used in accounting to determine the cost of producing identical products in continuous production processes. Itβs commonly used in industries like chemicals, textiles, food, and oil refining, where goods pass through multiple stages or processes before completion. Key Features of Process Costing: Mass Production: Suitable for products produced on a large scale. Uniformity: All units are identical and follow the same production process. Cost Allocation: Costs are assigned to each process or department rather than individual units. Average Cost Calculation: The total cost is divided by the number of units produced to get the cost per unit. Steps in Process Costing: 1οΈβ£ Collect Production Costs: Direct materials, direct labor, and overhead costs are gathered for each process. 2οΈβ£ Assign Costs to Processes: Each production stage (e.g., mixing, refining, packaging) is treated as a cost center. 3οΈβ£ Calculate Average Cost per Unit: By dividing the total process costs by the total units produced. 4οΈβ£ Transfer Costs: At the end of each stage, costs are transferred to the next process until the final product is completed. 5οΈβ£ Prepare Cost Sheets: A final cost sheet summarizes all costs and units produced. Industries Using Process Costing: Textile Industry: Processing fabric through stages like spinning, weaving, and dyeing. Oil Refining: Crude oil refining into gasoline, diesel, and other products. Food Production: Mass production of items like canned goods, snacks, and beverages. Example: If a company produces 10,000 liters of paint in a month and incurs total costs of βΉ5,00,000, the cost per liter would be: βΉ5,00,000 Γ· 10,000 = βΉ50 per liter. #ProcessCosting #CostAccounting #AccountingBasics #CommerceStudents #FinancialManagement #LearnAccounting #AccountingConcepts #BusinessAccounting #AccountingTips #StudyWithMe #CostingMethods #CommerceEducation #StudentLearning #AccountingForBeginners #ProcessCostingExplained #FinanceStudies #ManagementAccounting #OnlineClasses #AccountingLife #commerceclasses process costing,process costing in hindi,ca inter process costing,process costing one shot,process costing example,process costing numerical questions,equivalent production in process costing,commerce specialist,process costing normal and abnormal loss,introduction to process costing,process costing all concepts,video lectures on introduction to process costing,process costing ca inter,process costing for b.com,process costing cost accounting,process accountprocess costing,process costing in hindi,ca inter process costing,process costing one shot,process costing example,process costing numerical questions,equivalent production in process costing,process costing normal and abnormal loss,introduction to process costing,process costing all concepts,video lectures on introduction to process costing,process costing ca inter,process costing for b.com,process costing cost accounting,process account,equivalent units